Price is an inevitable factor when purchasing any type of technology, but when it comes to portable data collection can you really put a price on quality and reliability? Knowing where to spend more, and where you can afford to save some of your budget – without
experiencing damaging side effects to your business – can be a tough call.
Today, we’re presenting five reasons you can’t afford not to choose Miovision Scout for your portable data collection needs.
Comparing Scout based on price, misses the mark
When Miovision Scout gets compared with other cameras, as it often does, the price-gap between us and the other guys is obvious. But to limit the comparison to cost alone leaves out the key differentiators that more than make up for the difference in price. Its success in the market is no accident: We’ve incorporated over a decade of customer feedback, engineering expertise, and quality assurance into every Miovision Scout camera we ship.
Get the project done right the first time
Anyone that deploys equipment in the field, or manages a team of people who do, knows that in-field complications or equipment re-deployments cost huge amounts of time and money. Plus, it can devastate timelines, potentially delay projects, and add significant stress to get the job done. Miovision customers include engineering firms, data collectors, cities, counties, and DOTs that know saving a few bucks today isn’t worth the risk to their projects and their reputations tomorrow. That’s why we build Scout with an unmatched passion for quality and reliability.
Here are five ways that we guarantee quality and reliability for our customers:
1. Anti-fogging camera
What is the actual cost to repeat a count? Missed customer timelines, crews back out in the field, and extended project times not only cost money, they can negatively affect your reputation. We know that cameras will fog when exposed to varying temperatures, and foggy cameras can ruin a count and force redeployment. Off the shelf cameras are susceptible to moisture from relative humidity in the manufacturing facility, and by ingress from the elements over time. That’s why Miovision Scout cameras are assembled in house.
Our cameras are assembled in an airtight chamber, sealed with epoxy, then injected with nitrogen. This process removes any existing moisture and seals it from ingress, while the nitrogen adds a lower condensation point better suited to broad temperature ranges. So customers from Alaska to Dubai know they can count on Miovision Scout to handle extreme weather conditions with ease.
We also perform a two-part, pre-shipment quality assurance test on our cameras for humidity and water ingress:
- The first part is a humidity test in our environmental chamber. To test humidity levels we use a special lens cooling fixture that cools the lens rapidly to a set temperature, then visually inspect for condensation.
- The second part is a water ingress test. In this test, cameras are connected and programmed to record for 72 hours while they are submitted to simulated rainfall.
2. Quality control
Failed components can take units completely out of commission. That’s why the quality of our printed circuit board (PCB) is paramount. As the heart and brain of Scout, if the PCB quality isn’t assured, it may result in lost video or removing a unit from the field completely, costing potentially thousands of dollars in lost counts. That’s why we perform the following series of tests on all of our circuit boards, before they ship:
Environmental Stress Screen (ESS)
100% of the circuit boards manufactured are stress tested in an environmental chamber cycling between -40°F to 185°F (-40°C to 85°C). A single record failure on any board results in a Non-Conformance Record (NCR) and the part is quarantined for assessment to repair or scrap.
Printed circuit board in circuit test
By their nature, PCB’s have many potential points of failure. This is why we’ve invested in an In-Circuit Test (ICT) fixture, which tests every circuit, chip, and component.
Printed circuit board integrated systems test
An Interconnect Stress Test (IST) is performed by heating a sample board to 150°C (302°F). From there, the bare board is microsectioned and inspected using scanning electron microscope (SEM) images. The test is performed to establish a reliability expectation and determine the expected field life by means of accelerated testing. Scouts are tested at 350 cycles, meaning IST heats a sample coupon to 150°C (302°F), and then we microsection it and inspect it for issues. In fact, this test meets military standards.
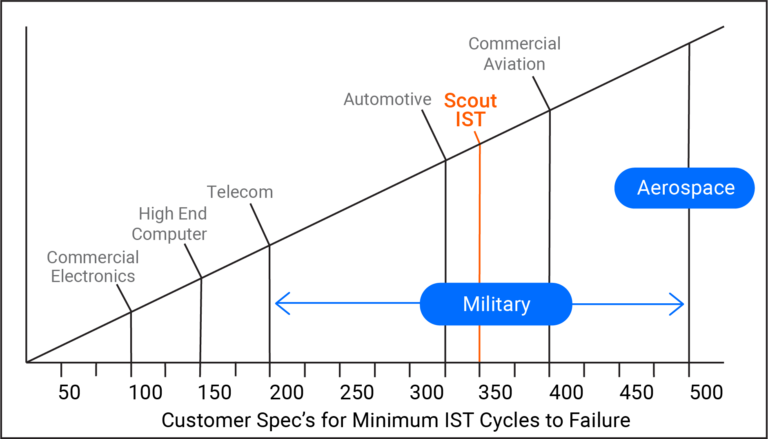
Unit burn-in test
Before any Scout unit leaves Miovision, it’s subjected to 720 burn-in cycles over 72 hours to simulate several years in the field. This means the test effectively replicates 720 field deployments – which amounts to deploying Scout roughly twice a week for 45 weeks a year, for a total of 9.5 years – to ensure that each Scout unit can withstand the type of usage it will experience in the field. The whole process consists of (i) Turn On, (ii) Boot Up, (iii) Proceed on Schedule, (iv) Engage at Correct Time, (v) Save to SD Card, (vi) Shut Down, (vii) Ensure Files are Written Correctly.
The tests we have in place, as detailed above, allow us to take proactive measures in case we determine any issue impacting Scout reliability. If issues are identified, they’re resolved before any Miovision Scout units are shipped, minimizing failures in the field.
3. Purpose-built user interface
The modern Scout Firmware is the product of months of user research, including many in-field visits by our Product Management team. It was developed and launched with a few important goals in mind:
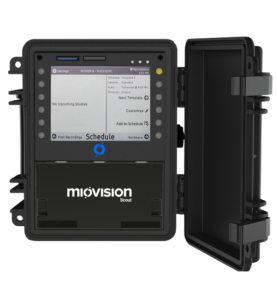
- Reduce time spent at the roadside.
Miovision Scout units are portable and durable,and can be installed at the roadside in just minutes, keeping field techs out of harm’s way. And, because they’re connected, teams can remotely change study requirements, monitor studies, and even receive notifications if something requires attention.
- Ensure hardware is set up for success.
Once the mast is fully extended, users can check to ensure Scout has a full view of the study area. Furthermore, Scout verifies if there is enough SD card memory and battery capacity to complete the upcoming study recordings.
- Catch errors prior to equipment take-down.
Video recordings can be reviewed quickly and easily prior to dismantling the equipment – allowing users to check for traffic anomalies or other study interference. In the unlikely event of a video recording failure, Scout logs battery and firmware information for review by our Customer Support Team. This allows customers to immediately schedule another recording, remotely, while our Customer Support Team identifies the root cause and takes steps to prevent a recurrence.
4. Remote monitoring and management
All Miovision Scout units are fully connected, allowing teams to remotely manage their devices. And, Miovision customers have access to the world’s only end-to-end traffic data platform: the Miovision DataLink platform. It’s the industry’s quickest and easiest way to request, deliver, and analyze traffic data, and houses all the traffic data and insights you need, all in one place.
5. Customer support
It can be very debilitating when experiencing a hardware issue in the field, which is why our Customer Support Team is the best in the industry. In fact, we have a 9.55/10 customer satisfaction rate on closed cases.
Response times
While we go to great lengths to ensure the quality and reliability of each and every Scout unit we ship, we know issues can still come up. That’s why we guarantee the following response times to ensure someone is there to help when you need it. Our team of highly specialized Customer Support Team will respond to emails within four business hours, answer phones in 120 seconds, and reply to voicemails in 30 minutes – or less.
Advanced replacement to reduce downtime
As part of our Limited and Extended Hardware Warranties, Miovision offers the Advanced Replacement Program. Customers simply notify our support team of a part that is damaged or needs replacement and we will ship it out immediately – ensuring their projects can stay on track. After receiving the replacement part, customers then have two weeks to ship us the failed part for repair or disposal.
Ready to take the next step? Get a quote for your Miovision Scout order.